Evaluating the Cost of Wood: Pricing Insights Per Square Foot
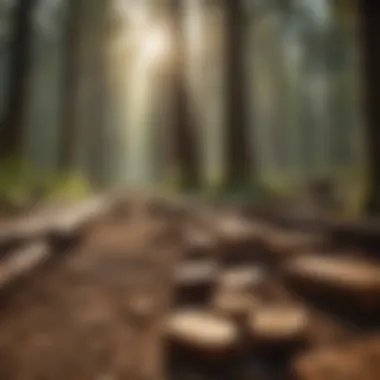
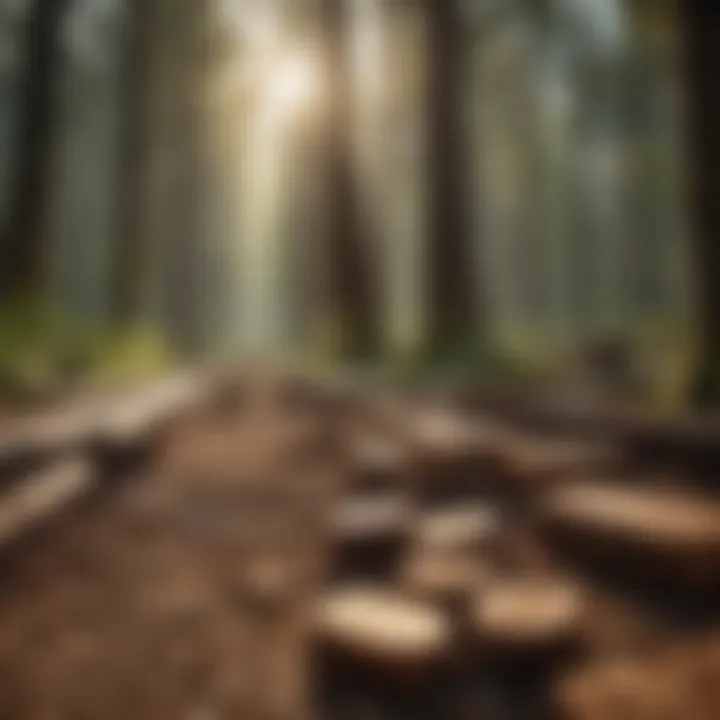
Intro
When considering the realm of wood usage in construction and forestry, understanding the associated costs per square foot becomes paramount. Many stakeholders, from builders to environmentalists, grapple with how pricing is shaped by myriad factors. This exploration will dig into everything from the different wood types available to regional pricing variations and the broader implications of sustainable practices.
Overview of Forestry Practices
- Definition of Forestry
Forestry encompasses the management and cultivation of forests, a practice that dates back centuries. It's not merely about cutting down trees; it's an intricate interplay of science, art, and environmental stewardship. Good forestry ensures that we maintain healthy ecosystems while providing necessary resources like timber. - Importance of Forestry in Ecosystem Management
Forests play a crucial role in maintaining balance within ecosystems. They contribute to biodiversity, mitigate climate change by sequestering carbon, and even regulate water cycles. Moreover, managed forests can yield economic benefits, supplying raw materials while preserving habitats.
Sustainable Forest Management
- Principles of Sustainable Practices
Developing sustainable forestry practices is fundamental for the longevity of our forests. This involves maintaining the health of the forest ecosystem while harvesting resources. Key principles include: - Techniques in Sustainable Management
Several techniques are utilized to promote sustainable management. Techniques can vary based on regional practices but generally include:
- Preserving biodiversity: By maintaining diverse species of trees and plants, forests remain resilient.
- Minimizing impact: Employing selective logging helps reduce damage to the remaining environment.
- Long-term planning: Sustainable practices necessitate thinking ahead, ensuring resources are available for future generations.
- Agroforestry: This integrates trees and shrubs into agricultural land, creating a symbiotic relationship.
- Controlled burns: These may be used to clear underbrush and promote healthier forest growth without compromising the ecosystem.
Woodland Stewardship Strategies
- Importance of Woodland Stewardship
Woodland stewardship is not just for landowners but for everyone who holds a vested interest in preserving our forests. Responsible management practices support ecosystem health and enhance the economic value of timber. The importance of custodianship in maintaining these vital resources cannot be overstated. - Best Practices for Landowners
For landowners looking to be good stewards, best practices could include:
- Regular assessments: Periodically evaluating the health of your trees and land can help in making informed decisions.
- Community involvement: Engaging with local forestry organizations can provide resources and support.
- Education: Continuously learning about forestry techniques keeps landowners informed about the evolving best practices.
In sum, approaching the cost of wood with an understanding of these broader practices sets a foundation for grasping the nuances of pricing per square foot. The confluence of sustainable practices with economic realities informs not only pricing strategies but also guides more profound stewardship of our forested landscapes.
Factors Influencing Wood Prices
In the realm of wood pricing, itâs imperative to understand what lies behind the numbers. The complexity of wood pricing is shaped by various interplaying elements, each carrying its weight in the final cost per square foot. Recognizing these factors can guide both buyers and vendors in making informed choices, enhancing the overall dynamics of the market. Price fluctuations can be attributed to species traits, market conditions, and quality metrics, making it essential to consider each aspect carefully.
Species Variations
Hardwood vs. Softwood
When discussing wood types, the distinction between hardwood and softwood is not just a technicality but fundamentally affects pricing. Hardwoods, like oak and maple, generally command higher prices due to their density and durability. They often exhibit intricate grain patterns that enhance aesthetics, making them popular for furniture and cabinetry. On the other hand, softwoods, such as pine and fir, are typically cheaper and faster to grow, thus making them a go-to for framing and general construction. The value-added features of hardwoods, alongside their longer lifespan, contribute to their elevated costs in comparison to softwoods.
However, hardwoods come with their own set of challenges, including difficulty in machining and higher maintenance requirements. Therefore, the choice between hardwood and softwood often boils down to the projectâs demands and budget constraints.
Exotic vs. Domestic Species
In this debate, the spotlight often shines on exotic species such as teak or mahogany, which not only bring unique visual appeal but also tend to carry a heftier price tag due to their rarity and importation costs. In environments where aesthetics are paramount, the allure of exotic wood can justify the expense. These species can deliver durability and rich colors, often making them a favored choice for high-end furniture or specialized applications.
Conversely, domestic species, like oak and poplar, provide a balance of availability, cost-effectiveness, and versatility. They are often more sustainable and readily accessible, driving their popularity for everyday projects. However, the exotic woods can lead to considerations around sustainability and ethical sourcing, adding layers to the decision-making process.
Market Demand and Supply
Current Market Trends
Keep a finger on the pulse of current market trends is essential for creating a sensible wood purchasing strategy. A surge in home renovations or increased housing construction can spike demand, pushing prices higher. As urban areas continue expanding, the pressure on wood supplies has increased significantly. The fluctuating costs also reflect seasonal trends; for instance, winter months may see a dip in prices as construction slows. Thus, understanding these currents can provide insights into the right time for purchases.
Moreover, the integration of technology in agriculture has enabled improved methods of cultivation and harvesting, influencing availability. When trends show a rise in sustainable building practices, the demand for certified wood products can also cause shifts in traditional pricing.
Impact of Supply Chain Disruptions
The impact of supply chain disruptions has shown itself in stark relief during global events, such as natural disasters or geopolitical strife. These interruptions can inhibit the flow of wood from producers to consumers, resultung in rampant price hikes. A recent example can be traced back to the pandemic, which not only affected transportation but also created labor shortages, exacerbating the existing demand-supply mismatch. Understanding these dynamics can serve as a powerful tool for anybody navigating wood procurement.
Thus, supply chain intricacies should not be underestimated. They directly correlate to the final pricing of wood while revealing the vulnerabilities within the industry.
Quality and Grading
Understanding Grades
Familiarity with grading systems is paramount for assessing wood quality and cost-effectiveness. Grading helps differentiate materials based on characteristics such as appearance, strength, and intended use, allowing purchasers to make well-informed selections. Generally, higher grades signify fewer defects and superior performance, subsequently commanding higher prices.
A common grading scale ranges from clear grade (the highest quality with minimal defects) down to lower grades that carry more knots and irregularities. The ability to discern these grades can make a significant difference in procuring wood that meets project requirements at a suitable price point.
Impact of Quality on Price
Lastly, the impact of quality on price cannot be overstated. Higher-quality wood, often found in hard-to-source species, is not just pricier but can lead to long-term savings given its durability and performance. Projects that prioritize longevity should consider investing in top-grade wood, which may initially seem expensive. However, the cost benefits can become apparent over time, as quality materials often require less maintenance and replacement.
Taking into account these multifaceted aspects of wood pricing equips buyers with the necessary insight to navigate their decisions wisely. Factors like species variety, market conditions, and quality expectations forge the overall landscape of wood prices, establishing a strategic groundwork for enhancing purchasing choices.
Standard Pricing Models
When delving into the world of wood pricing, understanding standard pricing models is essential. These models serve as frameworks for determining how costs fluctuate based on various factors, offering stakeholders a clearer lens through which to assess their budgetary needs. By grasping the specifics of these models, individuals can navigate the pricing maze more effectively, enabling them to make informed decisions around their wood procurement.
Cost Per Square Foot Breakdown
Average Costs Across Species
The aspect of average costs across species plays a pivotal role in understanding overall expenses related to wood. Different types of wood offer varied characteristicsâlike strength, aesthetic appeal, and durabilityâthat can significantly influence cost. For instance, softwoods such as pine often come in at a lower price per square foot compared to hardwoods like oak. This variation is crucial, particularly for projects that prioritize cost-effectiveness without compromising quality.
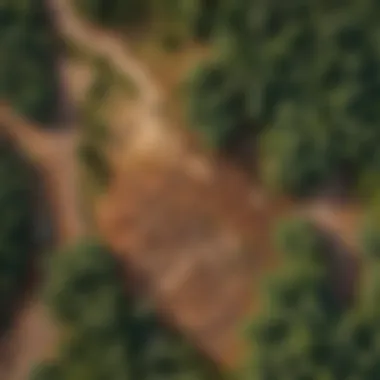
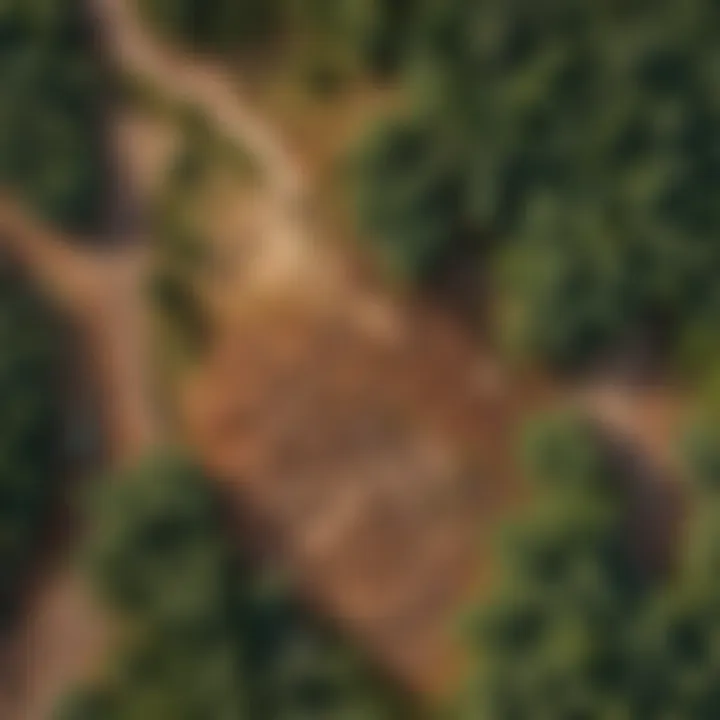
A key characteristic of average costs across species is its ability to inform project planningâa beneficial feature for budget-conscious consumers. By knowing what each type typically costs, professionals can avoid exceeding budget constraints or compromising on quality. However, itâs also important to recognize that cheaper options may not provide the best long-term value. Hereâs a look at both the advantages and disadvantages:
- Advantages:
- Disadvantages:
- Enables better budgeting for projects.
- Assists in choosing the right species for specific applications.
- Lower-cost options may require more maintenance or replacement sooner than pricier alternatives.
Regional Price Variations
Regional price variations are another significant aspect of how wood is priced per square foot. This concept hinges on where the wood is sourced from. For example, in areas with abundant pine forests, prices may be lower for pine compared to regions where hardwood is more common. The local demand and availability greatly affect the market prices, thereby influencing how much a contractor or buyer needs to pay.
The main draw of understanding regional price variations lies in its practical application during project planning. It allows individuals to assess whether sourcing wood locally could yield cost savings versus purchasing imported materials. However, while local sourcing often supports sustainability, it may also limit options. Hereâs a breakdown:
- Advantages:
- Disadvantages:
- Promotes local economies and sustainability.
- Potentially lower transport costs.
- Limited selection depending on sourcing location.
- Possible higher prices for rare regional species, even with local sourcing.
Factors to Consider in Pricing Models
Understanding factors to consider in pricing models is crucial as they can significantly affect the total cost of wood beyond just the price per square foot. Taking into account elements like volume discounts and delivery charges can provide additional insights into the actual costs involved in any wood procurement process.
Volume Discounts
One of the key factors to consider is volume discounts. When making a significant purchase, buyers often have the opportunity to negotiate lower prices per square foot based on the quantity of wood being ordered. Suppliers frequently offer discounts to encourage larger sales, which can result in substantial savings.
The notable feature of volume discounts is that they can incentivize bulk purchasing, thus reducing overall costs for projects that require large amounts of wood. This can be especially beneficial for contractors, who might have multiple projects in the pipeline. However, caution is warranted, as potential disadvantages include:
- Advantages:
- Disadvantages:
- Significant cost savings on larger orders.
- Better supplier relationships through repeat business.
- Potential over-purchasing if project needs are not correctly estimated.
- Cash flow may be impacted by large upfront costs.
Delivery Charges
Lastly, delivery charges can often be an overlooked aspect when evaluating wood pricing. While the cost per square foot might seem reasonable, adding delivery fees can substantially increase the overall expense. Delivery charges are influenced by factors such as distance from the supplier and logistics involved in the transport.
Recognizing these charges in the context of the total cost is beneficial for stakeholders. It underscores the necessity of factoring in all costs associated with procurement. Hereâs the upside and downside of delivery charges:
- Advantages:
- Disadvantages:
- Ensures that the actual price reflects comprehensive costs for budgeting.
- Allows for accurate comparisons when sourcing from different suppliers.
- Can significantly increase costs, affecting budget projections.
- Sometimes, additional costs come as surprises if not thoroughly checked in advance.
Through understanding these pricing models and their associated factors, stakeholders can gain a holistic view. This prepares them for better decision-making and project planning, ultimately ensuring that their financial investments in wood are aligned with their actual needs.
Comparative Analysis of Wood Types
Understanding the comparative analysis of wood types is essential for anyone making decisions about materials for construction, furniture, or crafting. By evaluating different wood species, stakeholders can better align their choices with project requirements such as budget, performance, and aesthetic appeal. Each wood type comes with its own set of characteristics that influence both price and utility, making it vital to thoroughly examine them.
Common Wood Species and Their Costs
Oak
Oak is often lauded for its strength and durability, which makes it a go-to choice for flooring, cabinetry, and furniture. It has a prominent grain pattern that is both striking and sophisticated, often seen in traditional and modern designs alike. The average cost for oak can range significantly, but it's generally considered mid to high tier in terms of pricing per square foot. Its density ensures a long lifespan; however, its weight can be a downside during installation, requiring more robust support structures.
Key Characteristics: Oak's versatility allows it to fit into various design schemes, whether rustic or contemporary. Most notably, its resistance to warping and denting stands out, which is why many homeowners and builders consider it a long-term investment.
"Every plank of oak tells a story of resilience; its strength is matched only by its beauty."
Maple
Maple wood is recognized for its smooth and even grain, which is ideal for both structural and aesthetic applications. Generally pricing a step below oak, maple is popular in furniture making and kitchen cabinets due to its lightweight nature and high resistance to scratches. Although hardwood, it does tend to feature a softer appearance compared to oak.
Unique Features: Maple can sometimes be finished with a high-gloss shine that enhances its natural tones. This wood type is often favored for its ability to keep colors bright and vibrant over time. However, it can be more susceptible to color changes if exposed to sunlight for extended periods.
Pine
Pine is one of the most economical wood options out there, making it a favorite among DIY enthusiasts and budget-conscious builders. It is lightweight and easy to work with, but its softer nature can lead to dings and dents more easily than oak or maple. The average cost per square foot is lower, which appeals to elementary and larger projects designed with cost efficiency in mind.
Considerations: Pine's grain and knots can create a visually rustic appearance, making it not only functional but also visually appealing for certain styles. Nonetheless, its softness can lead to a less durable finish, which is something to weigh for high-traffic areas.
Cedar
When it comes to outdoor use, cedar shines not just for its appearance but for its natural resistance to decay and pests. Though typically higher in price than pine, cedar's durability in external applications justifies the cost. It offers a pleasant aroma and a rich color that adds character to porches and outdoor furniture.
Advantages and Disadvantages: Cedar's light weight and inherent ability to withstand weather conditions make it popular, but it does require treatment to maintain its color and prevent fading. Considering these factors becomes vital when determining how to best utilize cedar in your projects.
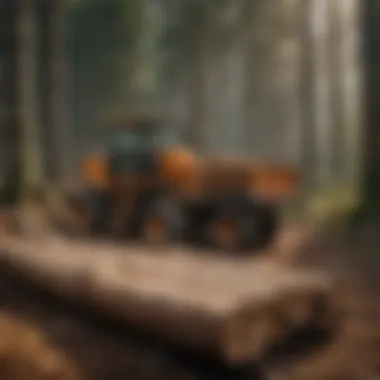
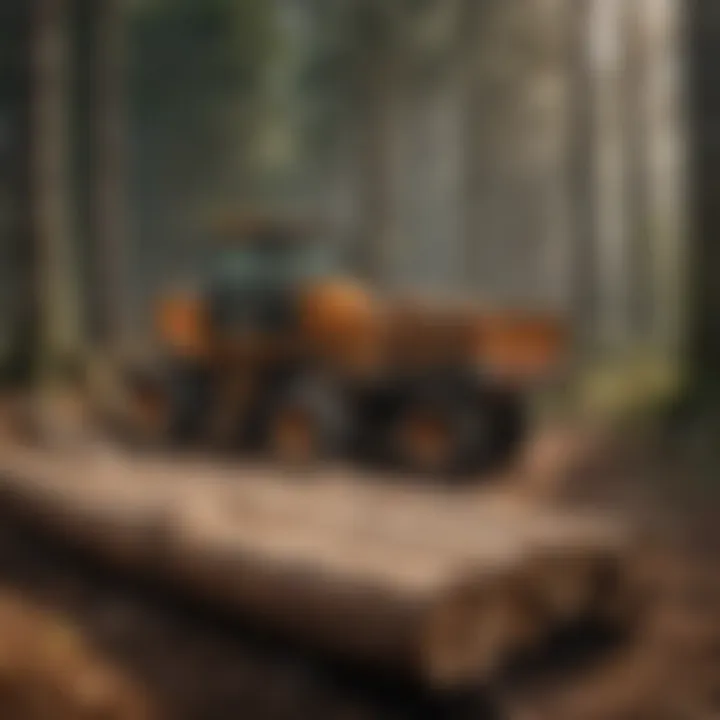
Emerging Wood Options
With the rise of sustainability concerns, newer wood materials are gaining traction.
Bamboo
Bamboo is increasingly recognized for being an eco-friendly alternative to traditional wood species. Fast-growing and renewable, bamboo can be harvested without causing environmental harm, positioning it as a future-forward choice in construction and design.
Key Characteristics: Itâs not just sustainable but also surprisingly strong, often outperforming steel in tensile strength tests. That said, it might not always provide the warmth in aesthetics that traditional woods do.
Reclaimed Wood
Reclaimed wood offers a blend of historical charm and eco-sensitivity. Sourced from old barns, factories, and other structures, it carries a story and character that new wood simply cannot replicate. While the prices can fluctuate based on rarity and quality, the allure of unique patterns and textures make it a compelling choice for design.
Considerations: One of the downsides is that reclaimed wood can sometimes come with hidden costs related to treatment and cleaning processes to ensure its safety and durability.
By comparing these wood types, one can get a clearer picture of their costs, benefits, and suitability for any given project. Not only does this knowledge empower informed decision-making, but it also lays the groundwork for budgeting wood purchases accurately.
Impact of Geography on Pricing
Understanding the geographical impact on wood pricing is like navigating a forestâyou can see the big picture but need to focus on the individual trees. The location from which wood is sourced plays a significant role in its cost, influenced by factors such as regional supply and demand, transportation costs, and even local regulations. In this article, weâll dissect how these elements intertwine to paint a clearer picture of what you might expect to pay per square foot.
Regional Differences in Wood Costs
Northern vs. Southern US Prices
When it comes to wood pricing, a fascinating aspect is the difference between Northern and Southern US prices. The Northern US is home to abundant hardwood species, like oak and maple; pricing is affected by heavy manufacturing and demand spikes during certain seasons. In contrast, the Southern US thrives with softwoods like pine and cedar, typically at lower costs due to the quicker growth rates of these tree varieties.
This regional divide affects everything from procurement costs to end-user prices. For instance, builders in the South often benefit from cheaper softwoods, making them a popular choice for framing and flooring. Conversely, prices in the North may escalate owing to higher transportation costs involved in shipping the denser hardwoods.
"Familiarity with local pricing nuances enables stakeholders to optimize their purchases across state lines and beyond."
International Comparisons
Diving into an international context can put things into perspective. The wood market isn't just a local affair but a global one. Countries like Canada, Brazil, and Sweden export significant quantities of wood, each adding its unique flavor to the price tags depending on local forestry policies and practices.
For example, Canadian lumber can come at a premium due to environmental regulations and sustainable practices implemented in their forestry sector. This focus on sustainability is increasingly appealing to eco-conscious buyers, even if it means higher prices. In contrast, wood imported from countries with less stringent practices may lower costs but brings up concerns about sustainability.
Local vs. Imported Wood
Wood sourced locally versus imported choices presents both challenges and benefits worth considering.
Benefits of Local Sourcing
One of the standout features of local sourcing is the reduction in transportation costs. Wood harvested nearby not only saves money but also helps local economies thrive. Local wood usually supports the community by creating jobs and sustaining local timber suppliers.
Moreover, buying locally often means shorter lead times, which is incredibly beneficial for ongoing projects or urgent needs. However, itâs important to note that not every locality has the same quality or variety of wood. This sometimes limits options for builders or craftsmen who have specific aesthetic or functional requirements in mind.
Environmental Considerations
Environmental considerations are increasingly crucial in todays wood market. Choosing local wood can significantly reduce the carbon footprint associated with transportation. Conversely, imported wood can sometimes leave a negative mark on the environment if it's not sourced sustainably.
Sustainability comes with its complexities. Imported wood might be cheaper but often leads to questions regarding deforestation and ecological damage in the exporting country. Balance becomes key here; weighing the benefits of cost against the potential environmental implications helps buyers make more informed decisions that align with broader sustainability goals.
In summary, geography affects wood pricing more than meets the eye. Local versus imported choices offer their own benefits, impacting not just the immediate project budget but also long-term environmental considerations. Understanding these elements thoroughly equips potential buyers to navigate the ever-changing landscape of wood pricing with confidence.
Additional Costs Related to Wood Use
When discussing the cost breakdown associated with purchasing wood, itâs crucial to think beyond just the initial pricing per square foot. Various factors entwined in the installation and maintenance of wood can significantly influence the overall financial commitment required. Not only do these costs impact budgets, but they also dictate the long-term viability and performance of wood products in a market thatâs ever-changing and full of unpredictability.
Installation Costs
Labor Expenses
Labor expenses stand as a major component of installation costs. Whenever wood is put to use in construction or renovations, skilled labor is necessary for proper handling, cutting, and fitting of the material. A key characteristic of labor expenses is their variability; skilled tradespersons may come with different rates based on their proficiency or regional market fluctuations. Due to this variability, itâs beneficial to seek multiple quotes from contractors to ensure a fair rate.
Another notable aspect is the time required for installation. The more intricate the woodwork, the longer it takes to complete, thus inflating labor costs. However, with proper planning and the right expertise, these expenses can be managed effectively. Engaging a skilled contractor can yield a quality finish that may save future costs linked to maintenance and repairs. Yet, on the downside, poor installation could lead to further expenses down the line, especially if issues like warping or misalignment occur.
Additional Materials
Additional materials are often necessary to complete a project involving wood. This includes items such as adhesives, fasteners, and finishing agents like paints or stains. The necessity of these materials can significantly impact the overall cost of a wood project. Itâs essential to recognize that while additional materials might seem like a minor expense upfront, they can amount to substantial sums depending on the wood type or the project's requirements.
One attractive characteristic of utilizing quality additional materials is their potential to improve both the durability and aesthetic appeal of the finished product. Quality stains can enhance the wood's natural beauty, while superior adhesives ensure long-lasting bonds. However, itâs also critical to balance the spending on these materials. Overextending in this area can lead to increased project expenses without necessarily providing a corresponding benefit, making it essential to know when to splurge and when to save.
Maintenance Costs
Long-term Upkeep
Long-term upkeep is another layer of costs many do not fully account for when they initially evaluate wood pricing. Wood requires more care than some other building materials, especially when it comes to its longevity and performance. Especially in environments with adverse weather conditions or high traffic, understanding the long-term maintenance ensures that the initial investment stands the test of time. This is a popular choice for conscientious buyers who aim for sustainability.
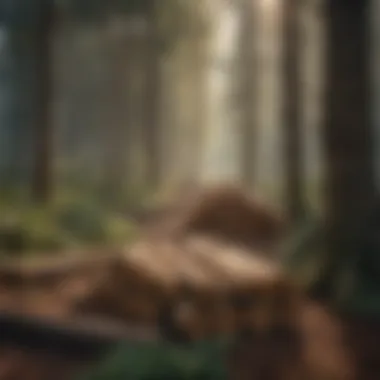
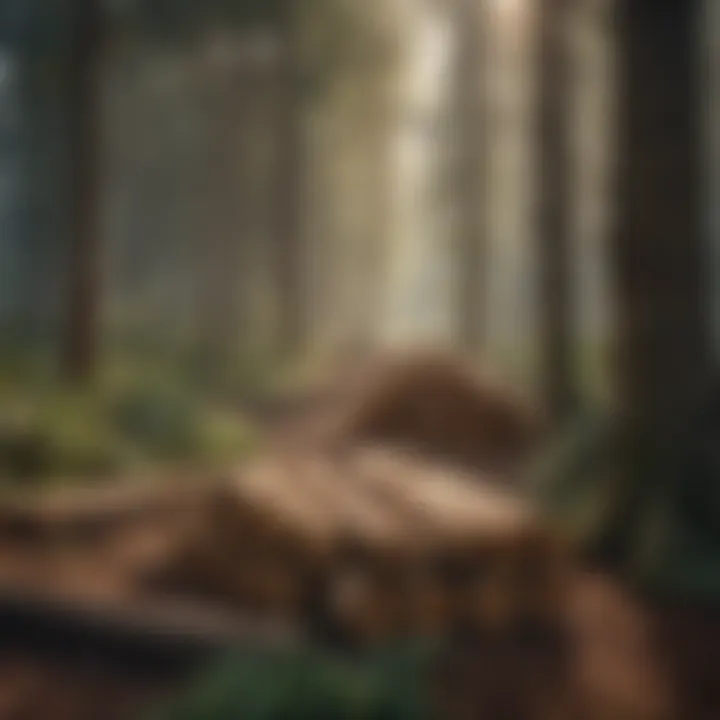
One unique feature of long-term upkeep is the variety of treatments and finishes available to wood. Regular maintenance might include refinishing, sealing, or treating the wood with protective coatings, which can add to the overall budget. Though these expenses can seem daunting at first, proper investments in upkeep can lead to avoiding larger replacement costs later on, which is a crucial consideration for those managing their expenses strategically.
Sustainability Considerations
Sustainability considerations play an ever-important role in modern woodworking decisions. Adopting eco-friendly practices is not just about meeting regulatory requirements; it also factors into long-term costs associated with wood use. Many consumers are now driven by a desire to make environmentally responsible choices, which influences wood selection and sourcing practices.
A key characteristic of sustainability considerations is their dual impactâenvironmentally and economically. Materials sourced from sustainable forests tend to come at a premium but offer peace of mind and potentially lower maintenance costs due to their inherent durability. Moreover, investing in sustainable practices helps mitigate waste that could incur details in disposal costs later on. In short, while the costs associated with sustainability might be higher up front, they can lead to significant savings in the long haul, aligning economic decisions with ethical values.
Best Practices for Budgeting Wood Purchases
When it comes to budgeting for wood purchases, small details can lead to big differences. An effective budget not only helps keep costs in check but also ensures that quality is not sacrificed for savings. Planning meticulously can shield one from unexpected expensesâlike a surprise bill popping up right when the project is heating up.
Setting a Realistic Budget
Evaluating Project Scope
Understanding the scope of a project is like drawing a roadmap before a long drive. When evaluators take the time to assess what their project entails, it lays the groundwork for creating a realistic budget. This encompasses everything from the size of the area needing wood to the design elements involved. The complexity of a project can vastly influence costs, making this assessment crucial. Consider how a more detailed layout can guide one to select specific wood types with appropriate pricing models.
- Itâs a beneficial practice as it contracts costs related to unexpected materials or labor.
- A good scope evaluation shows a clear path to purchase, which, in turn, can help towards effective negotiation with vendors.
One unique feature of evaluating project scope is that it lets buyers assess how much wood is needed, allowing for more accurate calculations of necessary expenses. Methods that aid in this evaluation can range from simple estimates to detailed architectural planning.
Inflation Considerations
Looking at inflation is essential for those budgeting wood procurement. Prices can shift dramatically over time, often due to external economic factors. Recognizing potential inflation trends helps professionals project future costs and thus can make better purchasing decisions today.
- This approach is incredibly beneficial because it helps avoid being blindsided by price increases.
- Understanding inflation may give one leverage when negotiating with vendors about pricing.
For instance, if the cost of lumber spikes due to a rise in demand, having this foresight allows for informed decisions on timing purchases before prices soar. This means a vendor's pricing strategy can be better understood, enhancing a buyer's ability to make strategic buying decisions.
Negotiation Techniques
When engaging in purchasing, strong negotiation skills often clinch deals that save substantial amounts of money. The negotiation process is as much an art as a science, involving understanding market rates and being aware of oneâs own needs.
Understanding Vendor Pricing
Familiarity with vendor pricing practices is fundamental to an effective negotiation. Different vendors come with their own rates, which can fluctuate based on a myriad of factors. Knowing these pricing metrics leads to more informed conversations. For example, vendors frequently offer different costs based on purchase volume or time of year.
- Understanding this aspect allows professionals to pinpoint budget allocation better.
- It effectively aids in reaping the best deals available for quality materials.
A unique feature of this knowledge is the ability to compare different offers without getting lost in jargon. In the end, the goal is to find the best price that still meets quality requirements.
Leveraging Bulk Orders
Finally, leveraging bulk orders can transform potential purchases into substantial savings. When done right, purchasing larger quantities at a discounted rate is can lower the per-unit price drastically. Many vendors are open to negotiation on bulk orders because it guarantees them salesâthey want to clear out their inventory just as much as you want to save on wood.
- The primary advantage rests in cost efficiency that favors large-scale projects.
- It can be a double-edged sword, however; thereâs a risk of over-purchasing, which can lead to waste if materials are not needed.
Being strategic about when and what to order in bulk can pay off significantly, but itâs crucial to do thorough assessments so that quantities align with project needs.
"Proper budgeting is about foreseeing the pitfalls and navigating through what you can controlâknowledge is power, especially in a market that's anything but predictable."
Finale and Future Outlook
As we tie together the threads of this article, understanding the landscape of wood pricing has never been more crucial for those involved in forestry and construction. This doesnât just affect wallets; it has implications on sustainability, local economies, and broader environmental initiatives. A clear grasp of pricing per square foot helps stakeholders make choices that align with both financial and ethical considerations.
Current Market Predictions
Expected Trends
With the persistent fluctuations in the wood market, keeping an eye on expected trends is key to navigating future costs. One of the most telling indicators is the growing preference for domestic over imported wood. This stems from a combination of environmental policies and shifting consumer preferences towards sustainability. As people become more aware of the carbon footprint tied to transportation, sourcing local woods appears not only as a practical choice but also a popular trend. It enhances the appeal of buying timber that doesnât travel thousands of miles, thus reducing emissions.
In particular, the rise in popularity of engineered wood products is reshaping the financial landscape. Engineered wood, such as cross-laminated timber, often brings cost savings, as it utilizes smaller trees and minimizes waste. This pushes prices down while also promoting more responsible forestry practices.
Potential Policy Impacts
Government policies play a pivotal role in molding market dynamics. Regulations aimed at protecting forests can often lead to tighter supplies, resulting in escalating prices. Tightening controls might be beneficial in enforcing sustainable practices, but can also inadvertently inflate costs for manufacturers and end-users alike.
Notably, tax incentives for using sustainable materials can shift the landscape. These policies are designed to encourage a shift towards more sustainable options while also fostering innovation in the industry. The takeaway here is clear: as policies evolve, so too must strategies for sourcing and budgeting wood.
Sustainable Practices Moving Forward
Promoting Local Sourcing
Promoting local sourcing is not merely a fad; it is becoming a necessity in todayâs market. Not only does it bolster local economies, but it also minimizes the environmental impact of transporting materials. When timber is sourced from local forests, it generally involves less handling and can be more affordable, contingent on supply and demand.
Moreover, local sourcing supports transparency in the supply chain. By being able to trace wood back to its roots, stakeholders can ensure that they are purchasing sustainably harvested timber. This benefits not just buyers, but the entire ecosystem around forestry and environmental advocacy.
Reducing Waste in the Industry
The timber industry has often been criticized for its wastefulness. Shifting towards practices that focus on reducing waste can present a compelling economic incentive. By implementing more effective manufacturing processes and better utilization of logs, companies can find cost efficiencies while conserving natural resources.
Waste reduction not only has the potential to lower costs but also enhances the overall reputation of the industry. In an age where consumers are increasingly scrutinizing environmental impact, showcasing a commitment to minimizing waste can ultimately serve as a competitive advantage.
"Understanding wood pricing is not just about evaluating dollars and cents; it connects to larger themes of sustainability and ethical sourcing."
In summary, moving forward, the industry stands at a crossroads, where informed choices about procurement and policy adaptations can influence not only individual projects but the forestry sector at large. A nuanced understanding of wood costs is vital not just as a standalone metric, but as a significant part of broader discussions around environmental sustainability and community resilience.