Understanding Refrigerated Trailer Costs and Factors
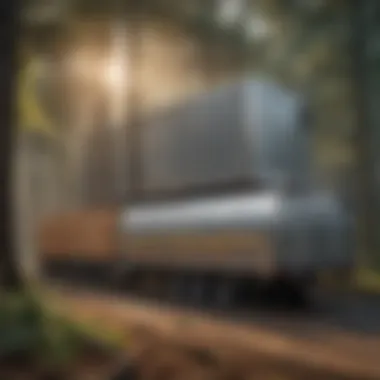
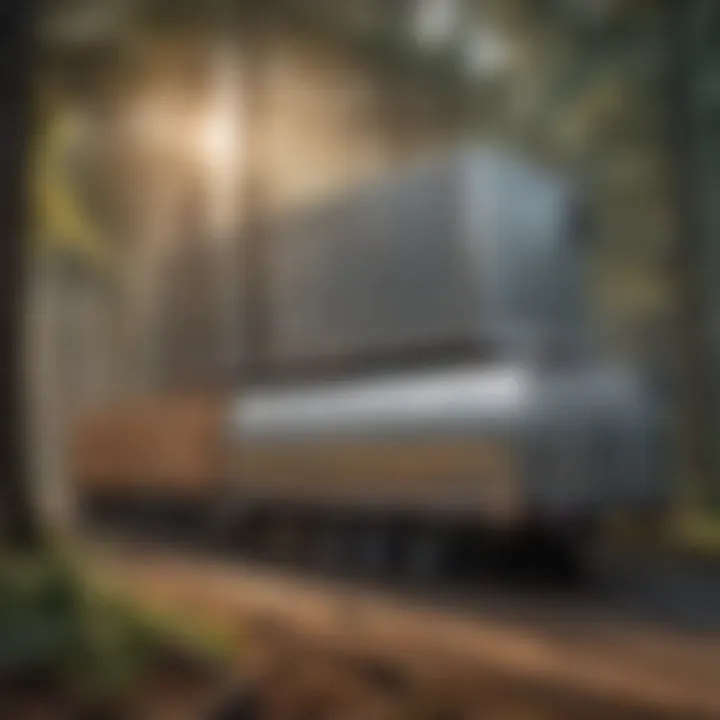
Intro
Refrigerated trailers, commonly known as reefer trailers, play a critical role in the transportation of temperature-sensitive goods. Understanding the costs associated with these trailers is essential for professionals involved in cold chain logistics. This section aims to provide a foundational insight into the financial considerations that shape the decisions surrounding refrigerated transport.
The key factors influencing the overall cost of refrigerated trailers include initial purchase price, ongoing operational expenses, maintenance requirements, and depreciation rates. Each of these factors interconnects to create a comprehensive financial landscape. More importantly, industry professionals must grasp these elements to make informed decisions that affect their logistics operations effectively.
In this article, we will explore various segments affecting the cost of refrigerated trailers in-depth. We will delve into the components that constitute the purchase price, highlight operational costs, and discuss the long-term financial implications of owning and managing these vehicles. The goal is to equip stakeholders with vital knowledge to navigate the complexities of refrigerated transportation economics.
Overview of Refrigerated Trailers
Refrigerated trailers play a crucial role in the cold chain logistics system. As a vital component, they ensure the safe transportation of temperature-sensitive goods such as food, pharmaceuticals, and other perishables. Understanding refrigerated trailers is essential not only for logistical efficiency but also for cost management.
By comprehending the intricacies of refrigerated trailers, stakeholders can make informed decisions both in purchasing and operational efforts, which can greatly impact profitability. The article delves into the types, purchase costs, ongoing operational expenses, and critical compliance factors related to refrigerated trailers, which are significant considerations for professionals in the industry.
In this section, we explore the definition and purpose of refrigerated trailers and detail their types, allowing readers to appreciate the diverse options available in the market.
Definition and Purpose
Refrigerated trailers, commonly referred to as reefer trailers, are specialized vehicles designed to transport goods that must be kept at specific temperatures. These trailers are equipped with refrigeration units that maintain the desired temperature, which can be essential for preserving the integrity of perishable items during transit. The primary purpose of refrigerated trailers is to provide a controlled environment that prevents spoilage and maintains product quality.
Types of Refrigerated Trailers
Different types of refrigerated trailers cater to various shipping needs. Understanding these variations is crucial for choosing the right type for specific goods and temperature requirements. Below are some prominent types of refrigerated trailers:
Single Temperature Reefer Trailers
Single temperature reefer trailers are designed to maintain a single temperature throughout the cargo space. This type of trailer is particularly efficient for transporting goods that require the same storage condition, such as fruits or vegetables. A key characteristic of these trailers is their simplicity in design, which often leads to lower operational costs.
One significant advantage of single temperature trailers is the relative ease of monitoring and maintaining the set temperature. It is a popular choice among businesses that have a steady flow of perishable items that do not require various temperature zones. However, the limitation is apparent when needing to transport different products with distinct temperature needs, which can lead to inefficiencies.
Multi-Temperature Reefer Trailers
Multi-temperature reefer trailers are designed to handle goods that need varying temperature zones within the same cargo space. This capability allows businesses to transport a mix of products simultaneously without compromising their individual temperature needs. These trailers feature multiple compartments, each of which can be set to a different temperature.
A primary benefit of multi-temperature trailers is versatility, allowing logistics companies to optimize their loads better. However, this complexity can lead to higher operational and maintenance costs since more cooling units may be necessary to ensure that all temperature compartments function correctly.
Swap Body Refrigerated Containers
Swap body refrigerated containers are portable and can be easily exchanged between trucks and trains. Their design allows for quick transfers, facilitating efficient logistics operations. One distinguishing characteristic of swap body containers is their adaptability; they can be used for various modes of transportation.
The primary advantage of these containers is their compatibility with both refrigerated and ambient transport needs, making them a flexible option in supply chains. However, they may require specialized equipment for loading and unloading, which can add to infrastructure costs.
Understanding the types of refrigerated trailers helps in deciding the most appropriate equipment for specific cold chain needs.
Initial Purchase Costs
The initial purchase costs of refrigerated trailers are a significant aspect to consider for anyone engaging in cold chain logistics. These costs are often the largest single expense when acquiring a trailer. Understanding these expenses helps businesses plan their budgets effectively. The price of a refrigerated trailer varies based on numerous factors, which we will explore in detail. \
Key considerations include the characteristics of the trailer, such as its size and brand. Additionally, whether one chooses to buy new or used equipment can greatly impact the overall cost. Knowing these details is essential for making an informed decision.
Factors Influencing Purchase Price
Size and Capacity
The size and capacity of a refrigerated trailer play a crucial role in determining its purchase price. Larger trailers tend to cost more due to their increased materials and the technology required to maintain proper refrigeration. Capacity also relates to how much cargo can be transported, which can be a deciding factor for many business operations. Selecting the right capacity is essential as it directly affects operational efficiency.
A key characteristic of adequate size and capacity is optimal utilization of the trailer. A trailer that is too small may result in more trips and higher fuel costs, while one that is unnecessarily large could involve spending more on initial costs, with underutilization of space. This leads to higher operational costs per unit transported.
Brand and Model
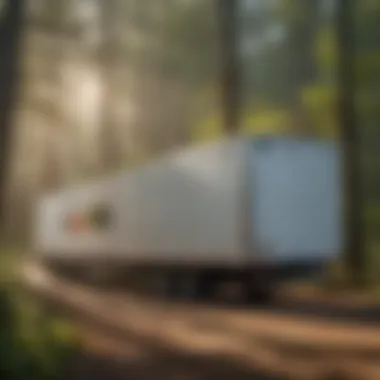
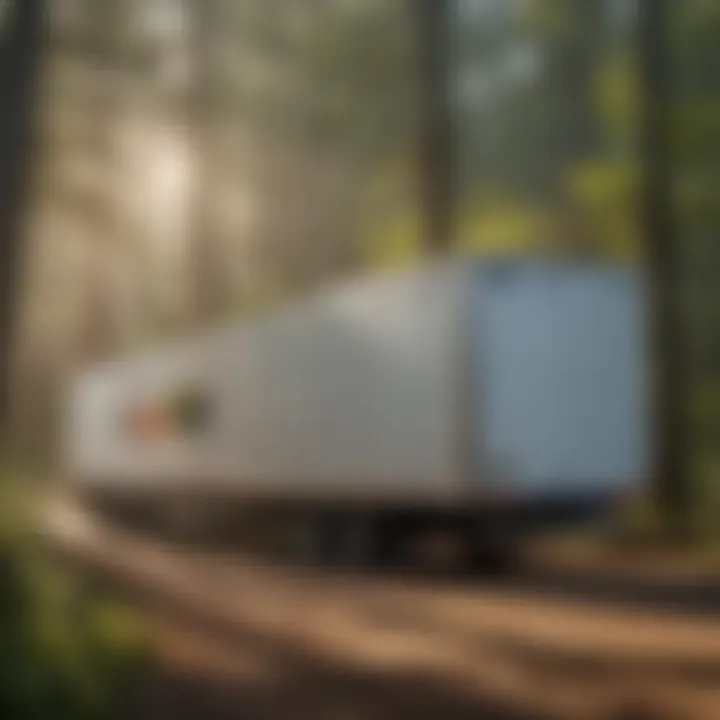
Brand and model are critical factors when analyzing the purchase price of refrigerated trailers. Renowned brands, such as Carrier and Thermo King, offer advanced features that may justify a higher price point. These brands are generally associated with reliability and performance, which can translate into cost savings over time. The reputation of a brand carries weight, especially when considering long-term investments.
Each brand often has unique features that resonate with users. For example, trailers from Carrier might feature advanced insulation technology that enhances fuel efficiency, while models like those from Utility Trailer Manufacturing are known for their durability and structural integrity. Making a choice based solely on price may overlook these valuable characteristics.
New vs. Used Trailers
Deciding between new and used trailers requires careful thought. New trailers come with the latest technology and warranty packages, which may offer peace of mind regarding potential repairs. A new reefer trailer is often customizable to meet specific business needs. However, the initial sticker price is usually higher than that of a used model.
On the other hand, used trailers provide a cost-effective alternative. The value of used trailers can be very appealing, especially for startups with tighter budgets. Nonetheless, buyers should be cautious as used models may not come with warranties, and their maintenance history is crucial to understand. \
The balance between purchasing new versus used trailers is about considering not only the initial costs but also long-term reliability and potential repair costs. Being well-informed about what both options offer will significantly assist in making the right choice.
Financing Options
Financing options can make a substantial difference in managing the cost of purchasing refrigerated trailers. Various pathways exist, such as loans, leasing agreements, and financing through manufacturers. Choosing a financial route influences the overall expenditure and cash flow. Careful review of terms and conditions is critical. Interest rates, repayment terms, and any prepayment penalties must be weighed against operational needs and projections.
Operational Costs
Understanding operational costs is essential for anyone involved in the logistics and transportation of goods, especially those that require refrigeration. These costs make up a significant part of the overall expenses associated with refrigerated trailers. This section will delve into the specific elements that constitute operational costs, the benefits of managing these costs effectively, and the considerations that must be taken into account.
Fuel and Energy Consumption
Fuel and energy consumption is a critical factor in the operational costs of refrigerated trailers. These vehicles rely on powerful refrigeration units which require substantial energy to maintain the necessary temperature for perishable goods. The type of fuel used—whether diesel, propane, or electric—greatly affects the total operational expenses.
- Fuel Efficiency: Different trailers have varying fuel efficiencies depending on the make and model. High-efficiency trailers consume less fuel, which can lead to lower costs over time.
- Energy Costs: Energy expenses can particularly rise based on fuel prices and the efficiency of refrigeration units. For instance, using a more modern trailer with advanced technologies like variable speed drives can reduce energy consumption. Regular fuel and energy audits should be conducted to identify areas where savings can be achieved.
Labor and Driver Expenses
Labor costs are another significant component of operational expenditures. Skilled drivers command higher wages, which can impact the overall budget. Additionally, driver expenses encompass various elements.
- Wages: Competitive wages are essential for attracting and retaining experienced professionals.
- Training: Investing in proper training for drivers can lead to reductions in accidents and improve safety, ultimately reflecting positively on the operational costs.
- Regulatory Compliance: Ensuring that drivers meet all regulatory requirements may incur additional costs, such as periodic training sessions and certifications.
Simultaneously, optimizing delivery routes can reduce the time drivers spend on the road, leading to lower fuel consumption and increased productivity.
Insurance Considerations
Insurance is a fundamental aspect of operational costs that should never be overlooked. It protects businesses against potential losses resulting from accidents, theft, or damage to goods in transit.
- Types of Insurance: Businesses need different types of insurance, including liability, cargo, and collision insurance. Each type caters to specific risks associated with refrigerated transportation.
- Premium Costs: Premiums can vary greatly depending on several factors such as the type of trailer, the value of the cargo, and the company’s claim history. Thus, shopping around for the best coverage is essential.
"Insuring a refrigerated trailer is not just a cost; it’s a vital investment in safeguarding your business against unforeseen events."
By analyzing these aspects of operational costs, businesses can make informed decisions that not only enhance efficiency but also contribute to overall profitability. Emphasis must be placed on tracking these expenses closely, as effective management can lead to substantial savings.
Maintenance and Repair Costs
Understanding the costs associated with maintenance and repair of refrigerated trailers is essential for any operator in the cold chain logistics industry. These expenses can significantly impact the overall profitability of transporting temperature-sensitive goods. Proper maintenance not only extends the lifespan of the trailers but also ensures compliance with regulations regarding food safety and quality. An effective maintenance strategy can mitigate unexpected repair costs, minimize downtime, and enhance operational efficiency.
Regular Maintenance Practices
Regular maintenance is crucial for the optimal performance of refrigerated trailers. It involves systematic inspections, adjustments, and replacements to keep the trailer in top condition. Key practices include:
- Routine Inspections: Regular checks on the refrigeration unit, seal integrity, and overall structural condition can identify issues early. This can prevent costly repairs later on.
- Cleaning: Cleaning of the refrigeration system, trailer interior, and exterior helps maintain hygiene standards, which is vital for food transport. Dirty units can lead to inefficiencies and increased energy costs.
- Lubrication: Keeping moving parts lubricated reduces friction, which helps prevent mechanical failures and extends the life of components.
- Refrigeration System Maintenance: Regularly checking coolant levels, and ensuring that the compressor and condenser are functioning well is essential. Faulty systems can lead to temperature fluctuations, risking product integrity.
Aligning maintenance practices with manufacturers' guidelines and schedules can significantly enhance reliability and cost-effectiveness. Maintaining detailed records of maintenance activities also aids in tracking performance trends and future needs.
Common Repairs and Their Costs
Even with regular maintenance, repairs are occasionally necessary. Understanding typical repairs and their associated costs can help in budgeting and financial planning. Common repairs include:
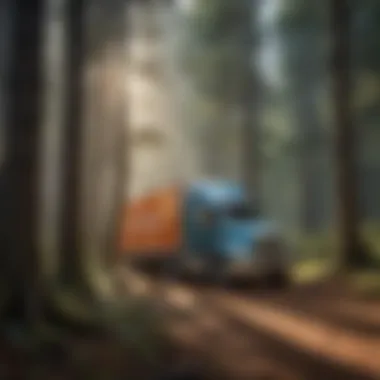
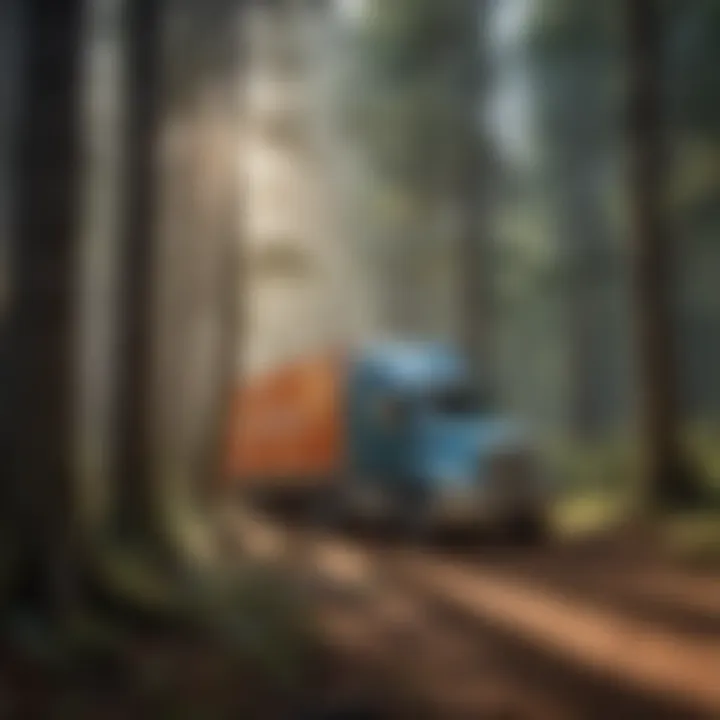
- Refrigeration Unit Repairs: Issues with the compressor, evaporator, or fan often require professional intervention. Costs can range from several hundred to thousands of dollars depending on the extent of the damage and the parts needed.
- Floor Repairs: The trailer floor can be damaged over time due to heavy loads or improper cleaning methods. Repairing or replacing the floor might cost anywhere from $200 to $1,500, based on severity and material used.
- Seal Replacements: Weather seals and door gaskets can wear out, leading to temperature control issues. Replacement costs usually hover around $150 to $400, depending on the number of seals needing replacement.
- Brake System Repairs: Brake components may require replacement due to wear and tear. Costs for brake repairs can vary widely, but a complete brake overhaul might approach $2,000.
Effectively managing maintenance and repair costs is critical in maintaining operational efficiency and ensuring compliance in cold chain logistics.
Depreciation of Refrigerated Trailers
Depreciation plays a crucial role in determining the long-term cost-effectiveness of refrigerated trailers. For professionals involved in cold chain logistics, understanding depreciation helps in making informed financial decisions. It impacts the value of the asset over time, affecting resale opportunities and financial statements. A clear insight into this topic can also provide a roadmap for budget planning and investment strategies.
Understanding Depreciation
Depreciation is the method of allocating the cost of a tangible asset over its useful life. For refrigerated trailers, the depreciation calculation considers factors like purchase price, expected lifespan, and maintenance routines.
The annual depreciation allows owners to predict the asset's decline in value. This insight helps when negotiating prices for selling or trading in trailers. A keen grasp of how depreciation works can lead to better forecasting and financial management in logistics operations.
Factors Affecting Depreciation Rates
Age of the Trailer
The age of a refrigerated trailer significantly affects its depreciation rate. Typically, the moment a trailer is purchased, it begins to lose value. The initial drop can be sharp. Generally, newer trailers retain more value compared to older ones. This is not just about age but also relates to the technological enhancements in newer models.
Older trailers, while they may be cheaper to purchase initially, often incur higher maintenance costs. Their cooling units might be less efficient, leading to increased operational costs. Thus, understanding the age factor helps fleets decide on whether to invest in new equipment or maintain older units.
Usage and Wear
Usage and wear directly influence the longevity and value of refrigerated trailers. Trailers that are used heavily or for longer routes face more wear and tear. Each mile traveled can reduce mechanical integrity and overall performance.
A highly utilized trailer may have a reduced resale value despite its age. On the contrary, trailers used sporadically may hold their value better over time. Regular inspections and maintenance are critical in managing wear. This can also extend their lifespan and ensure better ROI for the users.
Key takeaway: Understanding both age and wear offers valuable insights into managing recefer trailer investments efficiently.
Regulatory and Compliance Costs
Regulatory and compliance costs are critical considerations for anyone involved in refrigerated trailer operations. These costs can significantly affect both the operating budget and strategic planning efforts. Understanding the regulations that govern refrigerated transportation is vital, as they dictate the standards that must be met. Non-compliance can lead to penalties, forced modifications to equipment, or even temporary operational shutdowns. Thus, it becomes necessary to factor these expenses into overall cost calculations.
Industry Regulations Overview
The industry is subjected to a myriad of regulations, primarily established by governmental bodies and industry organizations. These regulations cover various aspects of refrigerated transportation, including:
- Health and Safety Standards: Ensuring that the goods transported remain safe and uncontaminated. This often involves temperature controls and monitoring systems.
- Environmental Regulations: Specifications regarding emissions and the use of refrigerants that may impact the ozone layer. Adhering to these environmental standards is essential for sustainability and minimizing ecological footprints.
- Transport and Logistics Regulations: These include specific mandates related to the operation of freight vehicles and how they manage temperature-sensitive cargo. It ensures that goods meet shelf-life requirements during transit.
Failing to comply with these regulations can lead not only to financial consequences but can also affect the reliability of a business in the eyes of its customers. Therefore, understanding regulations is necessary to maintain a competitive edge in the market.
Costs Associated with Compliance
Achieving compliance entails a variety of costs that operators must anticipate:
- Licensing and Permits: Obtaining necessary licenses and permits to operate legally within a certain jurisdiction incurs initial and possibly recurring expenses.
- Training and Certification: Employees may require training on compliance practices, safety standards, and operating procedures. This ensures that the entire team is knowledgeable about handling refrigerated units in accordance with the law.
- Upgrades and Modifications: Occasionally, existing refrigerated units may need technical upgrades to meet the latest standards. Modifications to existing equipment can be a significant financial undertaking.
- Regular Inspections and Audits: To ensure ongoing compliance, many industries require regular inspections conducted by third parties. Preparing for and undergoing these assessments also incurs costs.
Compliance is not merely a legal obligation but a commitment to professional integrity and operational excellence.
It is crucial to dissect these costs and understand the long-term investment they offer. Compliance ultimately ensures safer operations, reduces the risk of costly fines, and fosters trust among clients and stakeholders alike. By viewing compliance as an investment rather than a burden, businesses position themselves advantageously for a sustainable future.
The Role of Technology in Cost Management
Technology plays a significant role in managing the costs associated with refrigerated trailers. As the industry evolves, it becomes more crucial to implement efficient systems that can reduce both operational costs and enhance the performance of reefer trailers. In this section, we will discuss specific elements regarding monitoring and control systems, as well as the impact of advanced refrigeration technology on cost management.
Monitoring and Control Systems
Monitoring and control systems are essential tools for managing refrigerated trailer operations. These systems usually comprise software and hardware that track the temperature, humidity, and location of the cargo. By utilizing these systems, operators can detect any deviations from set parameters, which can prevent spoilage and loss.
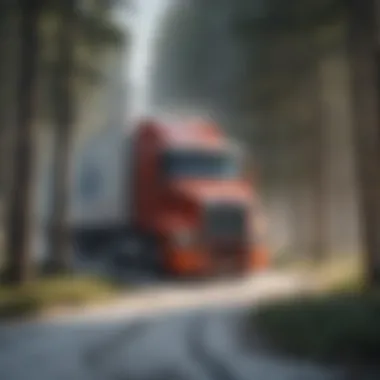
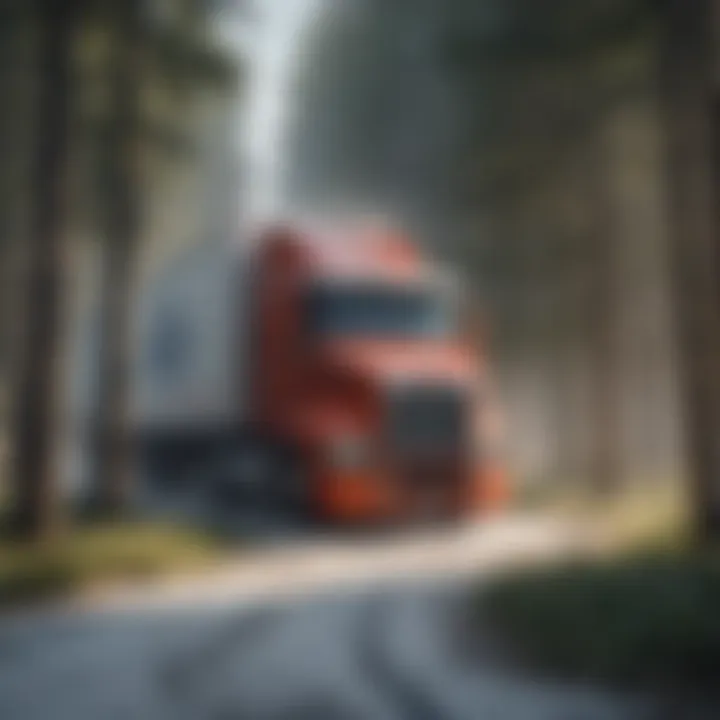
The benefits of implementing such systems include:
- Real-Time Data: Allows for immediate responses to any irregularities, such as temperature fluctuations.
- Efficiency Improvements: Helps optimize fuel consumption and reduce excessive wear of the trailer's refrigeration unit.
- Predictive Maintenance: Assists in anticipating maintenance needs before issues occur, thereby reducing downtime and repair costs.
"Informed decisions originate from timely data; monitoring technologies offer visibility that is vital for operational efficiency."
Moreover, integration with fleet management software can further streamline operations, ensuring that every aspect of the refrigeration process is accounted for and managed effectively.
Impact of Advanced Refrigeration Technology
Advanced refrigeration technology has fundamentally changed the landscape for refrigerated trailers. Modern systems can now utilize energy-efficient methods that not only reduce operational costs but also promote environmental sustainability.
Key advances include:
- Variable Speed Compressors: These units can adjust their power usage based on the cooling demand, significantly lowering energy costs.
- Thermal Insulation Innovations: Improved insulation materials prevent outside heat intrusion, allowing trailers to maintain optimal temperatures with less energy.
- Smart Sensors: These devices enhance monitoring capabilities by capturing data that can lead to better decision-making.
The impact of these technological advancements extends beyond direct cost savings. They also contribute to improving the reliability of deliveries and customer satisfaction. The combination of efficiency and progress ensures that businesses remain competitive in a demanding market environment.
Market Trends Influencing Costs
Understanding the market trends surrounding refrigerated trailer costs is essential for stakeholders involved in cold chain logistics. In a landscape that is constantly evolving, awareness of these trends aids in making informed decisions. Whether purchasing new equipment or managing existing assets, knowing current market dynamics can mean the difference between profitability and loss.
Supply Chain Dynamics
The complexity of supply chain dynamics plays a crucial role in the pricing of refrigerated trailers. Factors such as demand fluctuations, shipping routes, and inventory levels directly impact the cost associated with these trailers. When demand for perishable goods spikes, shipping companies often experience pressure on their resources, leading to increased operational costs.
In addition, shifts in consumer behavior, particularly in the wake of global events, have redefined demand patterns. Retailers increasingly opt for just-in-time inventory strategies, requiring swift and reliable transportation. This highlights the need for more refrigerated trailers on the road, consequently influencing market prices due to increased demand.
Investments in logistics technology, such as real-time tracking and inventory management systems, also illustrate how efficiently the supply chain operates. Efficient supply chain management can lower the operating costs of refrigerated trailers, indirectly affecting purchase costs and necessary budgeting for potential buyers.
Economic Factors
Economic factors play a significant part in shaping the costs associated with refrigerated trailers. Key elements include inflation rates, fuel prices, and labor costs. When inflation rises, the costs of materials and manufacturing processes increase, which can lead to higher prices for refrigerated trailers. This may compel businesses to rethink their buying strategies or delay purchases.
Fuel price fluctuations affect not only operational costs but also the overall market. As fuel becomes more expensive, transportation firms must adjust their budgets, which can lead to higher rates for moving goods. This interferes with the pricing strategy for refrigerated trailers, as companies may seek more fuel-efficient models to mitigate costs.
Labor costs, a consistent factor in logistics, also affect the finance behind refrigerated trailers. The constant need for qualified drivers expands the financial burden on fleet owners. When labor costs increase due to shortages or regulatory changes, businesses may opt to invest more in technology, potentially pushing down the demand for additional trailers temporarily.
Understanding these market trends enhances decision-making for businesses relying on refrigerated trailers, providing insights that can guide future investments and operational strategies.
The End
In the exploration of refrigerated trailer costs, several critical elements surface that are integral to understanding the economics of cold chain logistics. This article delves into various financial aspects of refrigerated trailers, capturing the full scope of expenses involved in their purchase, operation, and maintenance. An appreciation for these costs is essential for effective financial planning and decision-making within the industry.
Firms must consider the initial purchase costs, which entails evaluating factors such as size, capacity, and the possible difference between new and used equipment. Additionally, operational costs, including fuel and energy consumption, play a significant role in ongoing expenses. This discussion does not overlook labor, driver expenses, and the often-overlooked implications of insurance.
"Understanding detailed costs allows businesses to enhance profitability while ensuring effective compliance with industry regulations."
Maintenance and repair costs add a layer of complexity, as regular upkeep is crucial for optimal performance and longevity of the refrigeration technology. Knowledge of depreciation is also necessary, providing insight into the resell value and the eventual return on investment.
Regulatory and compliance costs cannot be ignored, given their impact on overall budgeting. The fast-evolving technological landscape is redefining many aspects of logistics operations, ensuring better monitoring and more efficient energy use.
Market trends, influenced by supply chain dynamics and economic conditions, finalize the outline of costs associated with refrigerated trailers. Being aware of these trends allows businesses to adjust their strategies accordingly, ensuring they remain competitive and financially sound as conditions fluctuate.
Understanding these diverse facets of refrigerated trailer economics culminates in a more informed approach to managing assets, leading to better financial outcomes. For industry professionals, grasping these insights translates to improved operational efficiency and governance of costs, providing a competitive edge in the cold chain logistics arena.
Summary of Key Points
- Initial purchase costs depend on size, capacity, and condition of the trailer.
- Ongoing operational costs include fuel, energy, and insurance, which are substantial over time.
- Regular maintenance is crucial for longevity and efficiency of refrigerated trailers.
- Depreciation impacts the future resale value of the trailers.
- Compliance with regulations must be budgeted for as it affects operational costs.
- Emerging technologies influence cost management positively.
- Understanding market trends aids in strategic decision making.
Final Thoughts
Businesses that prioritize understanding these costs consistently achieve greater levels of efficiency and profitability. As the logistics landscape evolves, continual reassessment of costs and adaptation to new trends will be crucial for maintaining competitive advantage.
With the proper approach to managing these aspects, companies can thrive in an increasingly complex market, ensuring quality service and customer satisfaction while optimizing their investments in refrigeration technology.